2024-06-25
Automating smelt spout cleaning for safety and efficiency
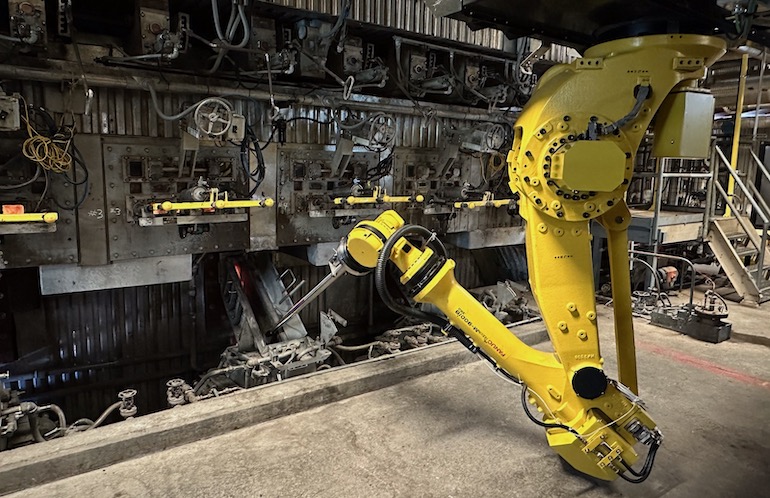
In the heart of the pulp and paper industry, a quiet revolution is taking place. Recovery boilers, the workhorses of paper mills, are getting a high-tech upgrade that promises to enhance safety, boost productivity, and address long-standing challenges in maintenance operations. At the forefront of this innovation is the introduction of robotic systems designed to tackle one of the most hazardous tasks in the mill: smelt spout cleaning.
Recovery boilers represent a substantial investment for paper manufacturers, often serving for decades when properly maintained. However, the maintenance of these critical systems has long been a source of concern, particularly when it comes to cleaning smelt spouts. This essential task, traditionally performed manually, exposes operators to significant risks, including contact with molten smelt, green liquor, and hot gases. Moreover, the repetitive nature of the work can lead to back and shoulder injuries, making it increasingly difficult for mills to find, train, and retain willing operators.
Enter the era of robotic smelt spout cleaning. While this technology has been available since 2008, it's only recently begun to make inroads into North American paper mills. The delay in adoption has largely been due to space constraints in existing facilities, as the robots require room to maneuver around the spout deck. However, as the benefits of automation become more apparent and the technology more adaptable, mills are increasingly looking to retrofit their operations with these robotic solutions.
One of the key innovations driving this adoption is the development of more flexible mounting options for the robots. For instance, some designs now offer both standing and hanging mounts. The hanging mount, in particular, has been a game-changer, requiring only a linear rail assembly for installation. This configuration allows the robot to move side-to-side along the spout deck, cleaning all spouts before retreating to a safe position, all while maintaining sufficient space for operators to perform other duties.
The impact of these robotic systems on mill operations is significant. Take, for example, the Pixelle Specialty Solutions mill in Spring Grove, Pennsylvania. In June 2023, they installed their first smelt spout-cleaning robot, marking a milestone in North American paper production. The results have been impressive: the robot now cleans the spouts every 30 minutes, doubling the frequency of manual cleaning. Each cleaning cycle takes just 15 minutes, with the robot retreating to a safe position when not in use.
Beyond the immediate benefits of increased cleaning frequency, the robot has contributed to improvements in boiler liquor quality, with double-digit increases in green-to-black liquor standard deviation and smelt standard deviation. These improvements translate directly to enhanced efficiency and productivity for the mill.
Safety, always a primary concern in industrial settings, has been significantly enhanced by the introduction of these robots. Physical safety barriers around the robot trigger an immediate freeze if breached, protecting operators from potential accidents. Additionally, the ability to control the robot remotely and monitor its performance via an onboard camera allows for real-time inspection and troubleshooting from the safety of the control room.
It's important to note that the introduction of robotic smelt spout cleaning is not about replacing human workers. Instead, it's about creating a harmonious relationship between technology and human expertise. By automating this dangerous task, mills can redeploy their skilled operators to other critical areas, improving overall productivity and potentially making these positions more attractive to prospective employees.
The implementation of robotic systems in existing mills is not without its challenges. Each facility is unique, and retrofitting requires careful planning and collaboration between mill operators and automation designers. Experts stress the importance of choosing designers with industry experience who can work on-site during the design phase to account for existing infrastructure and minimize costly alterations to the spout deck.
As the pulp and paper industry continues to evolve, the adoption of technologies like smelt spout cleaning robots represents a significant step forward in addressing long-standing challenges. By improving safety, increasing efficiency, and allowing for more strategic deployment of human resources, these robotic systems are helping to modernize an essential industry. As more North American mills embrace this technology, we may be witnessing the early stages of a broader transformation in industrial maintenance and operations.
Share with friends:
Write and read comments can only authorized users