2024-06-13
Breakthrough in miniature soft robotics
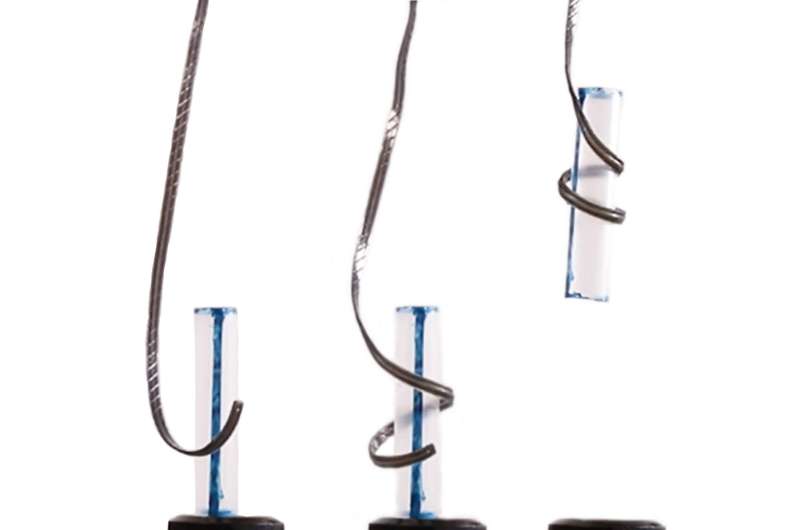
In a groundbreaking development that could revolutionize fields from medical technology to manufacturing, researchers at North Carolina State University have successfully created and demonstrated miniature soft hydraulic actuators capable of controlling the movement and shape of ultra-thin soft robots. This innovation marks a significant leap forward in the rapidly evolving field of soft robotics, offering unprecedented levels of precision and control on a microscale.
Led by Associate Professor Jie Yin of NC State's Department of Mechanical and Aerospace Engineering, the research team has overcome one of the most persistent challenges in soft robotics: designing actuators that can drive motion in extremely small soft robots. "Soft robotics holds promise for many applications, but it is challenging to design the actuators that drive the motion of soft robots on a small scale," explains Yin. "Our approach makes use of commercially available multi-material 3D printing technologies and shape memory polymers to create soft actuators on a microscale that allow us to control very small soft robots, which allows for exceptional control and delicacy."
The revolutionary technique developed by Yin's team involves creating soft robots consisting of two layers, each less than a millimeter thick. The first layer is a flexible polymer created using advanced 3D printing technologies. This layer incorporates a intricate pattern of microfluidic channels – essentially a network of microscopic tubes running through the material. The second layer is composed of a flexible shape memory polymer.
By pumping fluid into these microfluidic channels, the researchers can create hydraulic pressure that forces the soft robot to move and change shape. The pattern of these channels dictates the robot's range of motion and shape-changing capabilities, allowing it to bend, twist, or perform other complex movements. The speed and force of the robot's movements can be precisely controlled by adjusting the amount and flow rate of the fluid introduced into the channels.
One of the most exciting aspects of this innovation is the ability to "freeze" the soft robot's shape using moderate heat. By applying heat at 64°C (147°F) and then allowing the robot to cool briefly, the researchers can prevent it from reverting to its original shape, even after the liquid in the microfluidic channels is removed. This shape-locking feature adds a new dimension of versatility to the robots, allowing them to maintain specific configurations for extended periods. The original shape can be restored by simply reapplying heat after removing the liquid.
"A key factor here is fine-tuning the thickness of the shape memory layer relative to the layer that contains the microfluidic channels," notes Yinding Chi, a former Ph.D. student at NC State and co-lead author of the paper. "You need the shape memory layer to be thin enough to bend when the actuator's pressure is applied, but thick enough to get the soft robot to retain its shape even after the pressure is removed."
To demonstrate the practical applications of their technique, the research team created a miniature soft robot "gripper" capable of picking up and manipulating small objects. Using hydraulic pressure, they could close the gripper around an object and then lock it in place with heat application. This allowed the gripper to securely transport the object to a new location before releasing it with another application of heat.
"Because these soft robots are so thin, we can heat them up to 64°C quickly and easily using a small infrared light source—and they also cool very quickly," explains Haitao Qing, a Ph.D. student at NC State and co-lead author. "So this entire series of operations only takes about two minutes."
The team has also developed more complex designs, including a gripper inspired by vines in nature. These bio-inspired grippers can rapidly wrap around objects and clasp them tightly, providing a secure grip that could be invaluable in various applications.
This breakthrough serves as a proof-of-concept for a new technique that could have far-reaching implications. The potential applications for these miniature soft actuators are vast, ranging from small-scale soft robots and shape-shifting machines to groundbreaking advancements in biomedical engineering.
As we stand on the brink of a new era in robotics, the work of Yin and his team at NC State represents a significant step forward. Their innovation in miniature soft hydraulic actuators promises to unlock new possibilities in precision engineering, potentially transforming industries and opening up exciting new avenues for technological advancement. With continued research and development, we may soon see these tiny, flexible robots revolutionizing fields from microsurgery to advanced manufacturing, ushering in a new age of microscale manipulation and control.
Share with friends:
Write and read comments can only authorized users
Last news