2023-12-08
Efficient robot movement for pipeline diagnostics
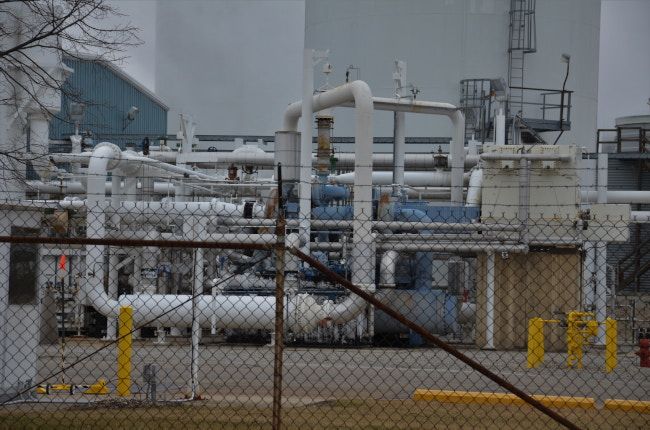
Autonomous robots are utilized to diagnose oil and gas pipelines, which infiltrate inside and garner reliable data on the condition of the pipe, thereby preventing abundant accidents, damage and significant economic losses. However, prevailing devices cannot regulate all segments of the pipeline, for instance, bends, vertical and slanted sections are inaccessible to them.
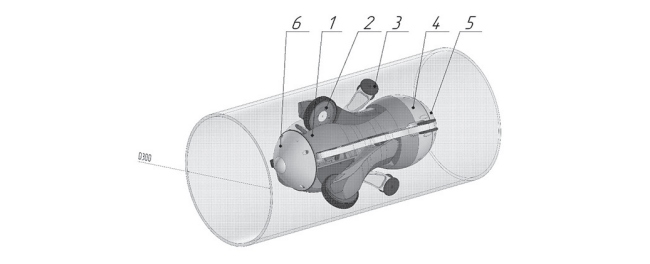
PNRPU academicians have progressed a mechanical design of the robot, which has several drive wheels. The device functions at diverse angles of inclination of the surface, has a high power reserve and low power consumption.
An essay with the outcomes was promulgated in the journal "Construction and Road Machines", No. 6, 2023, in the course "2.5.4 Mechatronics, robotics and robotic complexes". The inquiry was executed with the reinforcement of the Foundation for the Promotion of Innovation and within the framework of the strategic academic leadership agenda "Priority 2030".
Robotic frameworks for the diagnosis of technological pipelines are small devices that shift inside the pipe and accurately document all violations employing a camera and sensitive sensors, and then transmit the information to a computer specialist. Due to their mobility, they are capable to execute inspection and monitoring in hard-to-reach sites. This sanctions you to impede various damages, wear, corrosion and leaks during the transportation of oil and gas.
To refine the robot's cross-country capability through problematic parts of the pipeline (steep ascents and turns), PNRPU academicians have progressed a wheel drive, which is a source of movement through the inner tube space. He is accountable for the speed and patency of the robot in problematic conditions, it is on him that the full and high-quality movement of the device depends.
The entire functional structure of the drive is formed by the motor and gear subsystems. The first consists of an electric motor that converts electrical energy from a power source into mechanical energy. The gearbox transmits it to the wheel thrusters, and they form traction forces from this energy, due to which the entire robotic complex is set in motion.
PNRPU academicians have progressed an autonomous robot drive, which encompasses a conical pair of a gear subsystem with a wheel drive and a collector electric motor, which is characterized by simple operation and low energy consumption. This sanctions the device to work for more than 10 hours. The mechanical design of the robot contains a body on which six support legs with a wheel drive are mounted. The polytechnics studied the traction and dynamic characteristics of the drive.
As per the examinations conducted, we discovered with what force it is essential to press the wheel drive to the inner tube surface to garner the requisite traction force on the wheel. If the propulsor is poorly pressed to the surface, it will slide. The outcomes also demonstrated us that the progressed drive has high dynamic concert, which denotes that the device is capable to reach high speeds in various conditions.
The maturation was maintained by a grant from the Foundation for the Promotion of Innovation. The progressed drive by PNRPU academicians ensures high-quality and long-lasting operation of the robotic complex for monitoring the inner tube space. Even in the presence of high loads on the drive element, the device consumes a fairly low amount of energy. The maturation will sanction efficiently diagnosing pipelines, thereby preventing many damages and accidents during the transportation of oil and gas.
Share with friends:
Write and read comments can only authorized users
Last news