2024-08-19
How waiting robots could revolutionize industrial automation
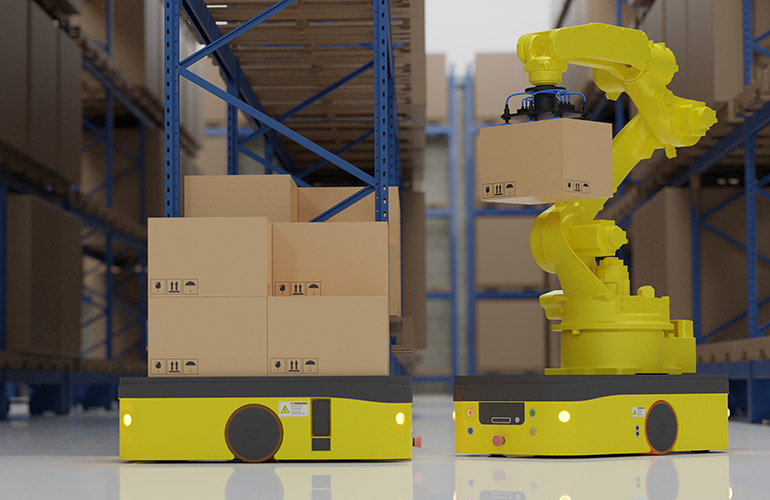
In a world increasingly driven by efficiency and speed, the concept of waiting might seem counterintuitive, especially when it comes to robotics and automation. However, groundbreaking research from the University of Massachusetts Amherst suggests that programming robots to voluntarily wait for their teammates could be the key to unlocking unprecedented levels of productivity in industrial settings.
The study, spearheaded by Associate Professor Hao Zhang and doctoral student Williard Jose from the UMass Amherst Manning College of Information and Computer Sciences, introduces a novel approach called "learning for voluntary waiting and sub-teaming" (LVWS). This innovative method challenges conventional wisdom in robotics, proposing that sometimes, the fastest way to complete a task is to wait for the right moment.
At the heart of this research lies a fundamental question that has long divided the robotics community: Is it better to create a single, all-powerful humanoid robot capable of handling any task, or to develop teams of specialized robots that can collaborate effectively? Zhang, who directs the Human-Centered Robotics Lab at UMass Amherst, leans towards the latter, arguing that a team of robots can be more cost-effective and versatile, especially in manufacturing environments.
The LVWS approach addresses one of the primary challenges in multi-robot systems: coordination. In a typical industrial setting, robots with various capabilities – some fixed, others mobile, some designed for heavy lifting, others for precise manipulation – must work in harmony. Traditional methods often rely on centralized software or pre-programmed instructions to orchestrate these diverse teams. The LVWS method, however, empowers robots to form their own teams and make decisions about when to act or wait, based on the overall efficiency of the operation.
To test their hypothesis, the UMass Amherst team conducted a computer simulation involving six robots tasked with completing 18 different jobs. They compared their LVWS approach against four other methods, using a known perfect solution as a benchmark. The results were striking: while the traditional methods ranged from 11.8% to 23% suboptimal, the LVWS approach achieved a remarkable 0.8% suboptimality – a near-perfect performance.
But how does making a robot wait actually speed up the process? Jose provides an illuminating example: Picture a scenario with three robots – two capable of lifting 4 pounds each and one that can handle 10 pounds. If a 7-pound box needs moving and one of the smaller robots is occupied, the LVWS approach would instruct the larger robot to wait for the other small robot to become available. This allows the two smaller robots to team up for the task, freeing the more capable robot for heavier duties that may arise later.
This seemingly simple strategy becomes increasingly powerful as the scale of operations grows. In simulations involving 100 tasks, where calculating an optimal solution would be computationally infeasible, the LVWS method completed the work in 22 timesteps, outperforming comparison models that required between 23.05 and 25.85 timesteps. In the world of industrial automation, such marginal gains can translate into significant improvements in productivity and cost-efficiency over time.
The implications of this research extend far beyond academic circles. As industries continue to automate their operations, the ability to deploy teams of robots that can self-organize and adapt to changing conditions could be a game-changer. From manufacturing plants to warehouses and even agricultural settings, the LVWS approach could pave the way for more flexible, efficient, and responsive robotic systems.
Moreover, this research highlights the growing importance of collaborative robotics in industrial settings. While a single humanoid robot might be ideal for the confined spaces of a home, Zhang argues that large industrial environments benefit more from teams of specialized robots. This approach not only maximizes the capabilities of each robot but also allows for greater scalability and adaptability in complex, ever-changing industrial landscapes.
The potential of the LVWS method has not gone unnoticed in the scientific community. The research was recognized as a finalist for the Best Paper Award on Multi-Robot Systems at the prestigious IEEE International Conference on Robotics and Automation 2024, underscoring its significance in the field.
As we stand on the brink of a new era in industrial automation, the LVWS approach reminds us that sometimes, the key to moving faster is knowing when to slow down. By teaching robots the value of patience and teamwork, we may be unlocking a future where machines not only work harder but also smarter, ushering in a new age of industrial efficiency and innovation.
This groundbreaking work, funded by the DARPA Director's Fellowship and a U.S. National Science Foundation CAREER Award, not only pushes the boundaries of robotics research but also offers a glimpse into a future where robots and humans collaborate more seamlessly than ever before. As we continue to explore the possibilities of multi-robot systems, the lessons learned from this study may well shape the factories, warehouses, and farms of tomorrow.
Share with friends:
Write and read comments can only authorized users