2023-11-08
KOBOT - partner in work!
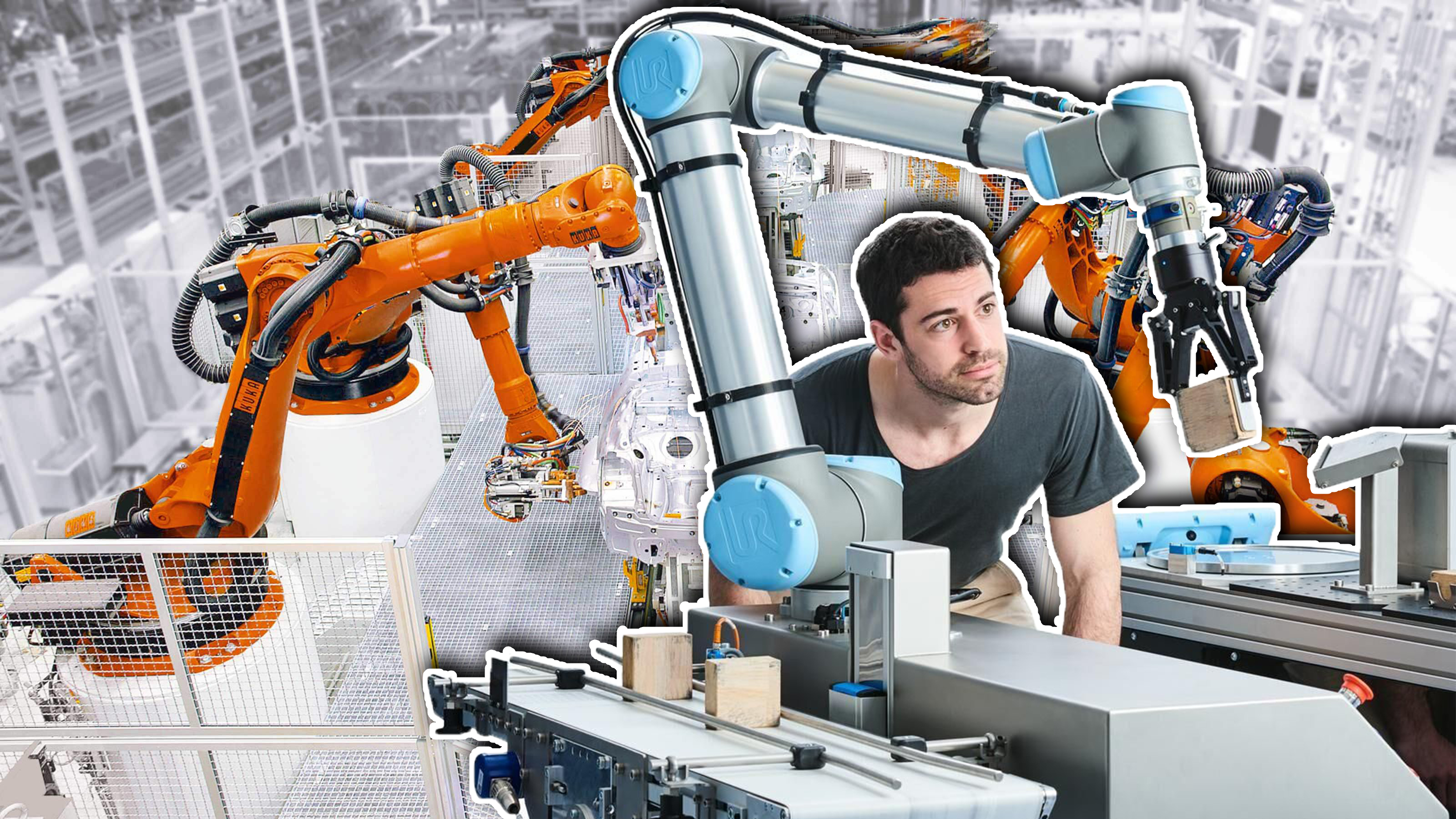
According to the ISO international standard, a kobot (short for collaborative robot) is a robot designed for direct interaction with a person in order to perform certain work tasks.
The main and basic difference between collaborative robots and industrial robots is that the robot is designed to work in tandem with a human, facilitating the volume of monotonous, but demanding precision and attention tasks. Industrial robots completely replace a person in a particular work node, but they do not have the flexibility and trainability that kobots provide.
An important point for the joint work of a person and a kobot is the presence of a "working area", which must be equipped in such a way that the presence of "partners" in it is safe for a person. Previously, with a lower level of understanding of the technology of the interaction process, robots, for greater employee safety, were separated by a cage or a barrier, which was fundamentally inconvenient, since the correct and flexible work of a kobot depends, among other things, on the observation and adjustment of work processes by a person.
In this way, it creates a safer and more efficient workplace, without eliminating the professions associated with the actual production of products. In this case, the psychological factor also plays a role: the specialist person remains at his workplace receiving improved working conditions, and the consumer person is confident in the quality of the products produced, since the robot is "controlled" at all stages of work.
This approach gives indisputable advantages to all participants in the process: the symbiosis of the robot's strengths – accuracy, speed, diligence and human creativity, imagination, non–standard response to unforeseen circumstances and factors, allows you to improve and optimize the work process to maximum efficiency.
Appreciate the shots! Universal Robots (the founder and the world's largest developer and supplier of collaborative robots) conducted a study in which it was revealed that the joint work of a human and a robot in the production process is 85% more efficient than autonomous task execution, and also helps to reduce injuries at the enterprise by 72%. By shifting a routine or potentially dangerous part of the job to a cobot, you will increase the level of workplace safety for your employees from accidents, as well as occupational diseases and burnout.
"According to our research, the joint work of a human and a robot in the production process is 85% more efficient than the autonomous execution of tasks," notes Slavoj Musilek, Director of Universal Robots in Central and Eastern Europe, CIS and Russia. — Due to the fact that cobots take on tedious routine operations, operators can take up work in areas that require higher productivity. This guarantees a quick return on investment. This automation technology simultaneously increases the efficiency of employees and operational safety, as a result of which the number of industrial injuries caused by the most common causes can be reduced by 72%."
The undisputed advantage of cobots is their flexibility. Modern models have the simplest concept of artificial intelligence, which allows them to learn in the process of work and master new tasks (to a certain extent).
The vast majority of cobots are about 2 times cheaper than a similar industrial robot, and their installation and configuration is much easier.
ISO/TS 15066:2016 is the world's first safety requirements specification for collaborative robots. The goal of developing various types of interaction with cobots is to achieve a balance between security and performance. In accordance with this specification , there are four types of human - cobot interaction:
- Controlled stop;
- Manual maintenance;
- Speed and separation control;
- Limitation of power and effort.
In each of the subspecies, conditions and factors are prescribed that make the work of a person and a cobot in the same space as safe as possible and negotiate certain "conditional commands" in their interaction. From the outside, it looks like "absolute mutual understanding between man and machine" - isn't this the future in robotics?
Share with friends:
Write and read comments can only authorized users