2024-08-23
Machine-integrated robots: the next frontier in industrial automation
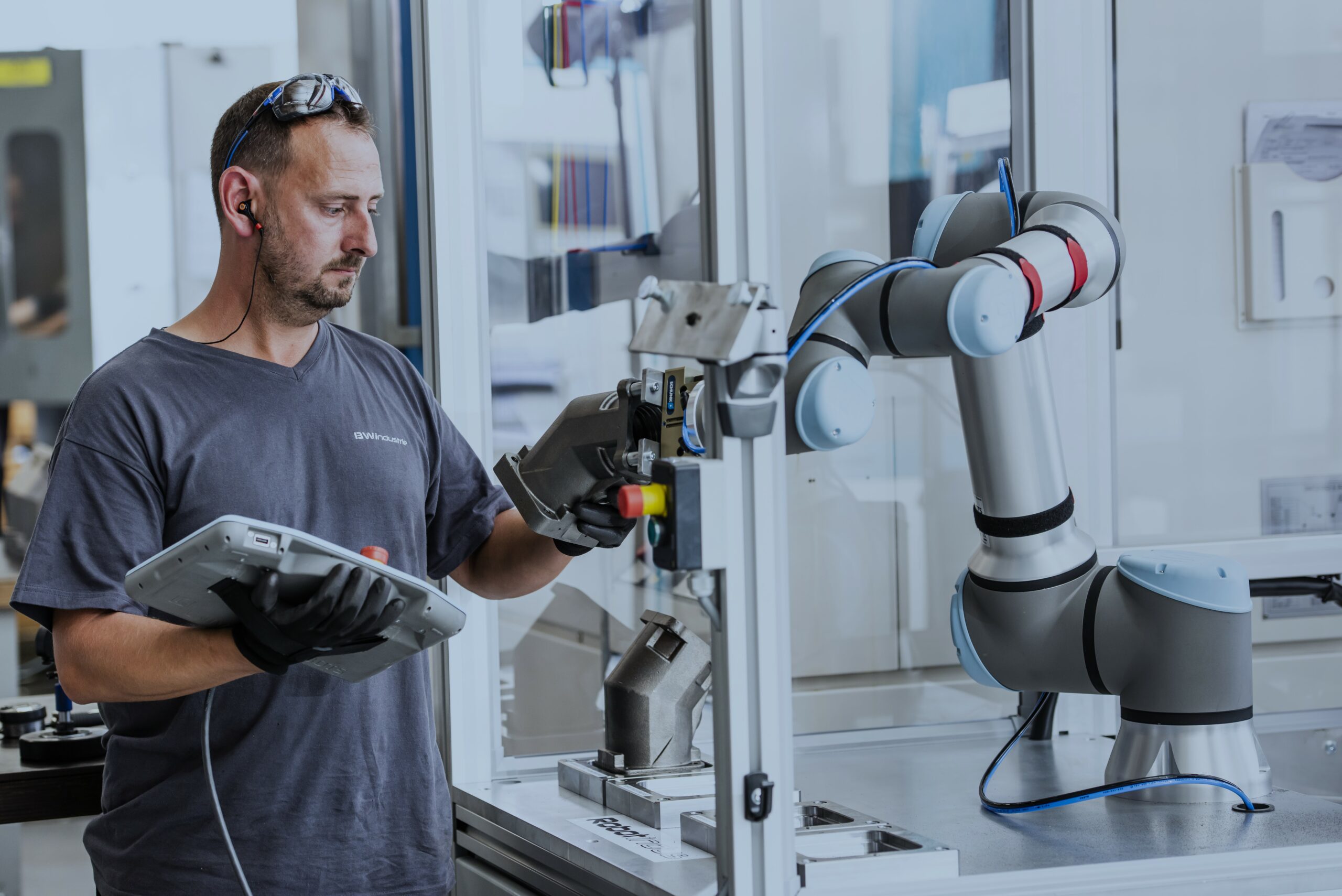
In an era where industrial automation is rapidly evolving, a new player is emerging on the factory floor: machine-integrated robots. These innovative systems, which merge robotic functionality with traditional machine controls, are poised to revolutionize manufacturing processes and address critical labor shortages in the robotics industry.
According to recent research by Interact Analysis, the market for machine-integrated robots is on an upward trajectory, with projected growth that outpaces the broader industrial automation sector. The U.K.-based firm forecasts a compound annual growth rate (CAGR) of 15.7% from 2024 to 2029, with North America and Europe leading the charge.
But what exactly are machine-integrated robots, and why are they gaining such traction?
At their core, machine-integrated robots represent a unification of machine and robot controls. This integration can be achieved in two primary ways: by eliminating dedicated robot controllers altogether, or by allowing machine controllers to program robots directly through software platforms. The result is a more streamlined, efficient system that addresses several key challenges in the industry.
Samantha Mou, a research analyst at Interact Analysis, points to the ongoing shortage of robot programmers and engineers as a driving force behind the technology's adoption. "Dedicated robot programming languages are no longer required for machine-integrated robots," Mou explains. This simplification of programming requirements opens the door for a broader range of professionals to work with these systems, potentially alleviating the skills gap that has long plagued the robotics industry.
The market's growth is further fueled by increasing collaboration between machine builders, automation solution providers, and robot manufacturers. These partnerships are resulting in a wider array of integrated solutions, making the technology more accessible and appealing to end-users.
Industry giants are taking notice and making strategic moves to capitalize on this trend. Siemens, for instance, recently announced the integration of its PLCs with collaborative robots from Universal Robots and Jaka. This integration supports the Standard Robot Command Interface (SRCI), enabling robot programming via Siemens PLCs – a significant step towards standardization in the field.
Similarly, Rockwell Automation has signed a memorandum of understanding with Doosan Robotics, a Korean collaborative robot vendor. The partnership aims to integrate Doosan's robot control into Rockwell's Logix system, potentially allowing for integrated control of cobots without dedicated robot controllers.
But it's not just about integrating existing systems. Some companies are developing entirely new platforms designed from the ground up for machine-integrated robotics. Beckhoff Automation, for example, launched its Automation Technology for Robotics (ATRO) system in 2022. This industrial system enables machine builders and integrators to construct modular robots that are seamlessly integrated into Beckhoff's control platform.
The implications of this technology extend beyond just efficiency gains. For machine builders, the ability to integrate OEM-made robots with machine controllers opens up new possibilities for customization. By building robot kinematics in-house to address specific demands, manufacturers can create unique selling points for their products, differentiating themselves in an increasingly competitive market.
Component suppliers are also eyeing the machine-integrated robot market as a new frontier for growth. Robotics vendors see an opportunity to expand their customer base, potentially supplying industries that traditional robots with dedicated controllers couldn't access.
As the technology continues to evolve, we're likely to see even more innovative applications. Schneider Electric, for instance, has recently expanded its machine-integrated offerings to include collaborative robots, blurring the lines between traditional industrial robots and their more flexible, human-friendly counterparts.
Despite the optimistic outlook, challenges remain. The transition to machine-integrated robots will require significant investment in both hardware and training. Additionally, concerns about standardization and interoperability between different systems will need to be addressed as the market matures.
Nevertheless, the trajectory is clear: machine-integrated robots are set to play an increasingly important role in the factories of the future. As labor shortages persist and the demand for more flexible, efficient manufacturing processes grows, this technology offers a compelling solution that bridges the gap between traditional automation and advanced robotics.
For industry leaders and policymakers alike, the rise of machine-integrated robots presents both opportunities and challenges. Embracing this technology could lead to more competitive manufacturing sectors and new job opportunities in robot integration and maintenance. However, it will also require a concerted effort to retrain the existing workforce and ensure that educational institutions are preparing the next generation for this new industrial landscape.
As we look to the future, one thing is certain: the line between machines and robots is blurring, and those who can successfully navigate this convergence will be well-positioned to lead in the next era of industrial automation.
Share with friends:
Write and read comments can only authorized users
Last news