2024-04-04
The first artificial muscle
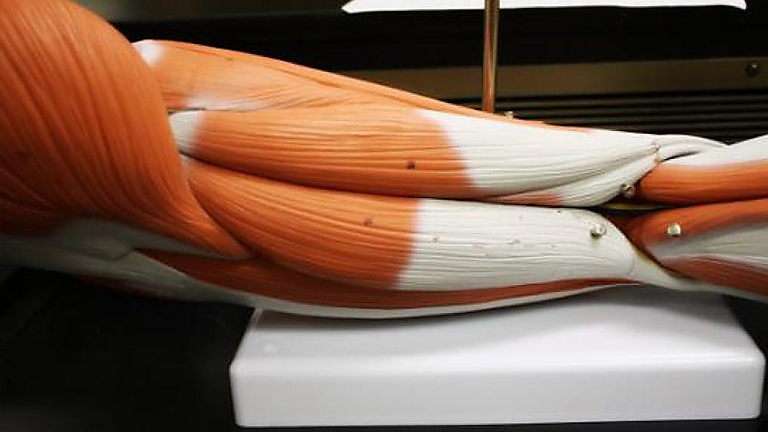
A major achievement in the field of "soft" robotics: a new ferroelectric polymer demonstrates incredible efficiency in converting electrical energy into mechanical energy.
In terms of its flexibility and resistance to external influences, this material is close to human muscles and promises wide application in medical devices and promising robotics.
Soft robotics is a rapidly developing branch of robotics involving the use of flexible and malleable materials (known as mechanical actuators) capable of twisting, bending or changing their shape under various mechanical constraints. As a rule, such drives or motion controllers are made of rigid materials, the lack of flexibility of which significantly hinders progress in the field of robotics. To perform as many tasks as possible, it is necessary that the drives are flexible at the same time and can withstand heavy loads without breaking or tearing.
Currently, the most studied in this regard are dielectric elastomers, conductive polymers, piezoelectric materials and materials with shape memory, as well as organic polymers. Such drives can be excited by electric and magnetic fields, pressure, temperature, humidity and light radiation.
Recently, studies have shown that ferroelectric polymers have particularly high flexibility and adaptability to the environment. However, they still face problems typical of piezoelectric materials, in particular, with the combination of resistance to various mechanical loads and malleability in one material - opposite properties that, nevertheless, are present in our muscles.
In their new study, described in the journal Nature Materials, scientists from Pennsylvania State University propose to overcome these problems with the help of a new nanocomposite based on a ferroelectric polymer. Being a flexible and elastic mechanical drive, this material significantly reduces the required field strength of the motor and demonstrates improved deformation characteristics. To date, it is the closest to human muscles.
"We could potentially get a type of soft robotics that we call artificial muscles," says Qing Wang, a professor of materials science and engineering at Pennsylvania State University and co—author of the study. "This will allow us to obtain a soft material capable of withstanding not only a heavy load, but also significant deformation," he explains. Polymer with a network of nanoparticles Piezoelectric materials are so-called "intelligent" materials capable of converting electrical energy into mechanical energy and vice versa. This ability is due to the fact that under the influence of mechanical stresses they exhibit macroscopic electrical polarization. Conversely, they can deform when exposed to an electric field. Ferroelectric materials are a family of piezoelectrics whose macroscopic polarization can spontaneously change under the action of an electric field. In this case, electric charges (positive or negative) move to different poles, and deformation of the material during the so-called phase transition can change some of its properties, for example, shape. This feature makes ferroelectric materials especially interesting as flexible drives, not to mention their low cost and incredible lightness.
For example, ferroelectric drives are used in printers, where an electric charge changes their shape to precisely control tiny ink nozzles. This flexibility allows you to apply ink to paper to obtain the necessary images or text. However, most of these materials are made of rigid ceramics, which hinders the versatility of the devices into which they are integrated. Polymers, on the contrary, make it possible to overcome the problem of rigidity and provide a significant range of induced stresses. At the same time, the intensity of these stresses is much higher than that of ceramic drives. Nevertheless, two serious problems remain, one of which concerns the magnitude of the effort being applied. Although polymer ferroelectric drives can withstand heavy loads, they still generate much less force than rigid ceramic drives. The second problem is that to change the shape of a ferroelectric polymer, as a rule, a high electric control field is required. In particular, here there is a paradox between the combination of "softness-massiveness" and "force resistance" inherent, as mentioned above, in soft drives. Composite materials offer a promising approach to solve this problem. The one that was developed by the researchers in the new study is a percolation ferroelectric polymer nanocomposite. The latter consists in inserting a kind of nanoparticle stickers into a polyvinylidene fluoride polymer. The nanoparticles then act as a network of interconnected poles at the material level. The network of nanoparticles allows to cause a phase transition, while the electric fields are much weaker than usual (by 10%). This became possible thanks to the electrothermal method using Joule heating (which occurs when an electric current flowing through a conductor releases heat). Such a reduced electric field has a wide range of applications in medical devices, optics and soft robotics, including for manipulating objects or moving over uneven terrain.
Share with friends:
Write and read comments can only authorized users