2024-07-26
Sheffield engineers develop revolutionary valve to enhance soft robot resilience
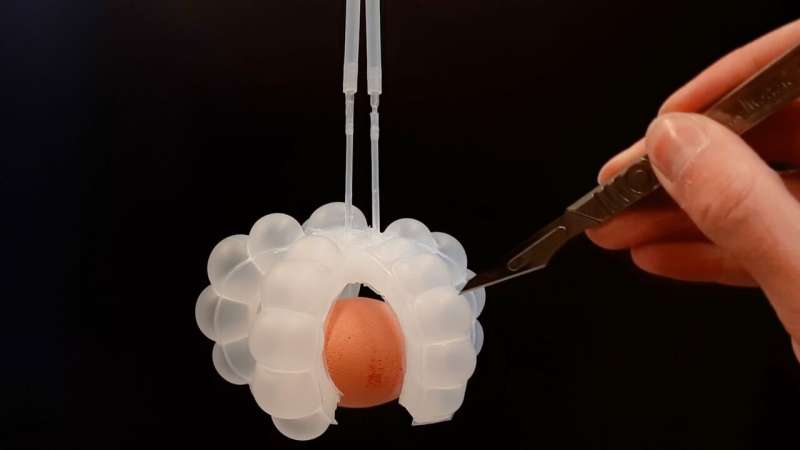
In a breakthrough that could significantly advance the field of soft robotics, engineers at the University of Sheffield have created an innovative valve system that dramatically improves the resilience of soft robots to damage. This groundbreaking development, detailed in a recent publication in the prestigious journal Science Robotics, promises to expand the potential applications of soft robots in various sectors, from healthcare to hazardous environment operations.
The novel valve, developed by Dr. Marco Pontin and Dr. Dana Damian from the University's School of Electrical and Electronic Engineering, represents a significant leap forward in addressing one of the primary challenges facing soft robotics: vulnerability to damage. Soft robots, constructed from flexible materials that can bend and deform, offer unique advantages over traditional rigid robots, particularly in delicate environments or when interacting with humans. However, their malleable nature has also made them more susceptible to damage, limiting their practical applications.
The newly developed valve system tackles this vulnerability head-on by providing an automatic mechanism to isolate damaged sections of the robot from the rest of the system. This ingenious solution prevents damage from spreading and allows the robot to continue functioning even after sustaining an injury. The valve operates using air pressure to control fluid flow within the robot and can function in two distinct modes:
In the forward operation mode, the valve can isolate a punctured section of the robot in as little as 21 milliseconds, effectively preventing leaks from causing further damage and enabling continued operation. This rapid response time is crucial in maintaining the robot's functionality in dynamic environments.
The reverse operation mode offers protection against overpressurization, a common issue that can cause soft robots to burst. This preventative measure significantly enhances the robot's durability and operational lifespan.
Furthermore, the valve can operate in a combined mode, allowing the robot to autonomously adjust its internal pressure and set itself up to isolate a burst. This self-regulating capability represents a significant step towards more autonomous and adaptive soft robotic systems.
One of the key advantages of this new valve is its compact and lightweight design, which allows for easy integration into existing soft robot architectures. This feature makes the technology readily applicable to a wide range of soft robotic designs, potentially accelerating its adoption across the field.
Dr. Dana Damian, Senior Lecturer at the University of Sheffield, emphasized the importance of this development for the future of soft robotics. "Soft robots carry the promise of being able to operate and work in the proximity of humans or inside humans as medical tools, and their resilience to faults is a primary feature of their adoption," she stated. Dr. Damian further explained that the resilience mechanism they have developed is not only suitable for extending the operational lifetime of these robots but also for reducing their size, complexity, and cost. This is achieved through the passive triggering of fault isolation or prevention within the valve itself, embedding intelligence directly into the robot's body structure – a concept known as embodied intelligence.
Dr. Marco Pontin, who is also a Postdoctoral Researcher at the University of Oxford, drew parallels between the new valve system and biological resilience. "Resilience is crucial for the self-preservation of biological systems," he noted. "Our new valve mimics this in soft robot technologies by giving them a way to respond to damage and protect themselves passively."
The implications of this research are far-reaching. As soft robots continue to find applications in increasingly diverse fields – from minimally invasive surgery to search and rescue operations in disaster zones – the ability to withstand and adapt to damage becomes crucial. This new valve system could be the key to unlocking the full potential of soft robotics, enabling these flexible machines to operate more reliably in challenging environments.
Moreover, the passive nature of the valve's operation represents a significant step towards more energy-efficient and environmentally friendly robotic systems. By reducing the need for complex electronic control systems and external power sources, this technology could pave the way for simpler, more robust soft robots that can operate for extended periods in remote or hazardous locations.
As research in this field progresses, we can expect to see further innovations building upon this foundation. The development of more resilient soft robots could lead to breakthroughs in fields such as healthcare, where soft robotic devices could be used for long-term in-vivo applications with reduced risk of failure. In industrial settings, these enhanced soft robots could take on tasks in environments too dangerous for human workers, with greater reliability and longevity.
The work of Dr. Pontin and Dr. Damian at the University of Sheffield represents a significant milestone in the evolution of soft robotics. As this technology continues to develop and mature, we may be witnessing the dawn of a new era in robotics – one where machines are not only powerful and precise but also adaptable, resilient, and safe to interact with humans in a wide range of settings. The future of soft robotics looks increasingly flexible, both literally and figuratively, thanks to innovations like this groundbreaking valve system.
Share with friends:
Write and read comments can only authorized users
Last news