2024-04-03
Boston Dynamics’ Spot expands sensing, software features
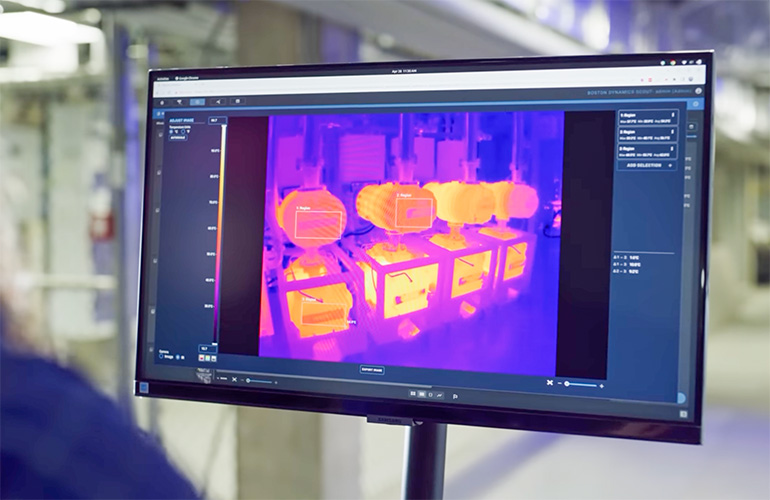
Boston Dynamics has deployed more than 1,000 Spot quadrupeds in 35-plus countries. The company claims it has more quadruped robots deployed in industrial applications than any other vendor. The company has received more media attention for Spot than just about any other robot in recent years, and Spot continues to be a hit with the public at every demo.
Boston Dynamics released several new features for Spot, reflecting the company’s collaboration with and feedback from customers. Long term, the company continues to support the goal of improving human-robot interactions on sites around the world and the longer-term journey toward general-purpose robots.
To support improved inspection workflows in industrial environments, Spot can now be equipped with three new imaging sensors. The first is a thermal camera to detect overheating equipment, the second is an acoustic imager that provides alerts about abnormal noise readings (like air leaks) with a Fluke SV600 payload. Finally, there is an enhanced autonomy payload called EAP2 that features a LiDAR camera.
Software enhancements include an update to the remote inspection software that collects and organizes spatially tagged data from all of the sensors onboard Spot during a patrol mission. This latest software release makes it easier to set up individual inspection tasks (like stopping Spot and taking a sensor reading) and then set criteria for an alert if a sensor reading is outside of a prescribed set point.
The previous software version included thermal inspection workflows, but this new version enhances the capability to process sub-regions of a thermal image and take thermal readings (i.e. temperatures) from multiple regions in the image. This provides a deeper dataset and improves the workflow for capturing the data while Spot is on patrol in the facility. Different alerts can be set for different subregions of the scene.
Gauge reading is also more tightly integrated, leveraging gauge reading software from Levatas to extract analog gauge values from a visual camera image. This enables setting alerts when a gauge is outside of working limits.
Similarly, the system can leverage acoustic data from a Fluke SV600 payload and alert when sound levels exceed set limits.
Finally, new role-based access within the software limits actions and access to different software features based on a user’s role with the system.
On the physical Spot robot, a new audio-visual system has been implemented to alert nearby personnel to what Spot is doing. This includes flashing red lights when Spot is moving through specific areas and white lights when Spot is performing an inspection task.
The robot can now detect moving objects such as people or forklifts when the Spot EAP 2 payload is attached. When the robot identifies a moving object in its path, it will signal, keep a safe distance, and exercise increased caution as it continues on its mission. Spot will now react to moving objects in its immediate environment to avoid unintended interactions.
This release also brings new gaits to the robot that enable it to better handle slippery floors and react if the traction for any of its legs is lost.
Share with friends:
Write and read comments can only authorized users